What is Masterbatch PET, its types and uses?
PET masterbatches are a combination of polyethylene terephthalate (PET) and various additives that are used in the plastics industry to improve the physical and chemical properties of plastic materials. These masterbatches can add properties such as heat resistance, transparency, mechanical strength and UV protection to plastics.
There are different types of PET masterbatches for various applications, including colorants, water-repellent additives, antistatic agents and UV protectors. These masterbatches are used in various industries such as automotive, packaging, electronics and sanitary ware, and help manufacturers create desirable properties in plastic materials and reduce costs.
Types of PET masterbatches and their applications
-
Colored masterbatches
-
UV-resistant masterbatches
-
Heat-resistant masterbatches
-
Antistatic Masterbatches
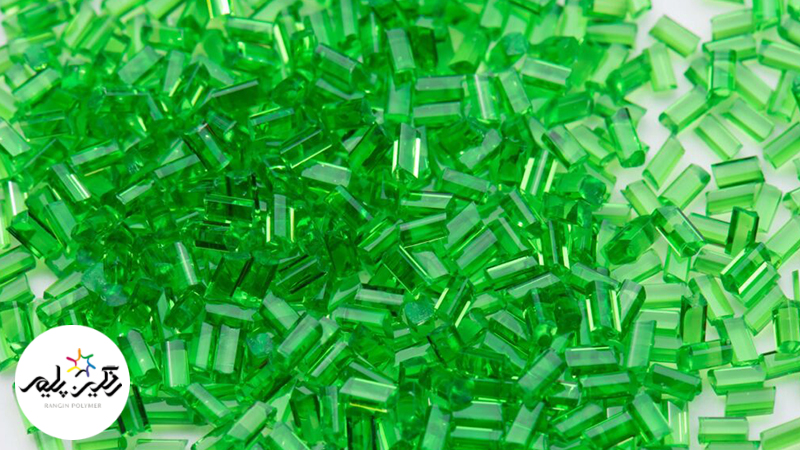
Improving the properties of plastics
Masterbatches, as advanced compounds, provide significant improvements in the properties of plastics. By using special additives added to masterbatches, various properties such as resistance to heat, UV radiation, static electricity and mechanical properties can be added to plastics. These additives increase the durability and lifespan of plastic products, so that plastics become more resistant to various environmental conditions such as high temperatures, sunlight and electrical effects. Also, various types of PET masterbatches allow manufacturers to add properties such as color, transparency and anti-impact performance to their products accurately and uniformly, which improves the final quality and their numerous applications in various industries.
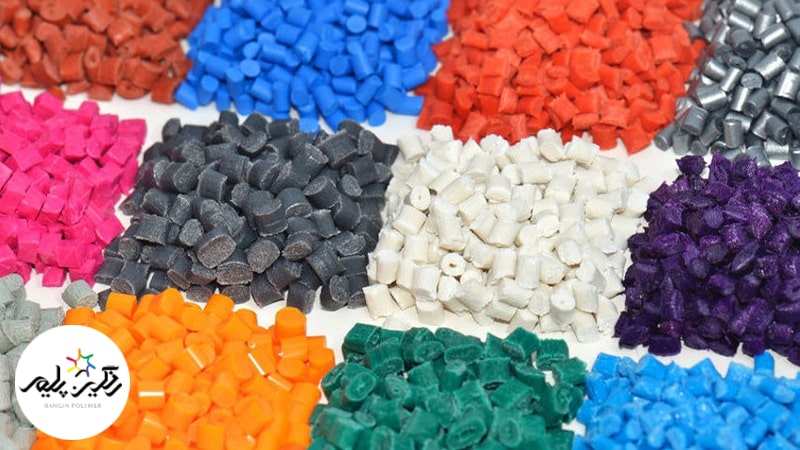
A solution to reduce costs and increase efficiency
The use of masterbatches is recognized as an effective solution in reducing costs and increasing efficiency in the plastics production process. By combining different additives and colors in a base material, there is no need to use each of these materials separately, which greatly reduces the costs associated with the purchase and consumption of raw materials. In addition, the production process using masterbatches is simpler and faster, because the materials are ready-made and carefully combined, and there is no need to add materials separately to the production line.
This process not only leads to a reduction in production time, but also higher accuracy in the use of additives and colors, leading to reduced waste and increased overall productivity. Rangin Polymer, as a manufacturer of various PET masterbatches, offers suitable economic plans in this field.
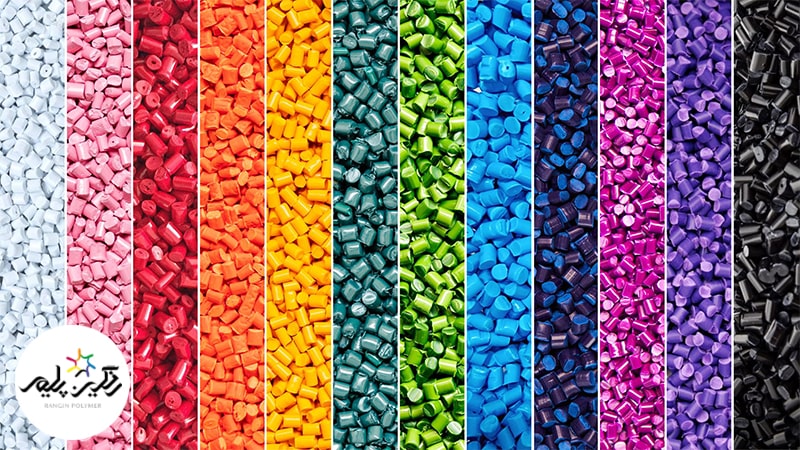
Mechanical and chemical properties of plastics
The mechanical and chemical properties of plastics are key factors in determining their performance and durability in various applications. Mechanically, plastics can have properties such as tensile strength, hardness, flexibility and impact resistance depending on the type of compounds and additives used. These properties can be significantly improved, especially by adding masterbatches, as these additives help to strengthen the molecular structure of plastics.
Chemically, plastics may have different resistance to environmental factors such as UV radiation, corrosive chemicals, moisture and high temperatures. Masterbatches can also improve these properties by adding special compounds such as anti-UV, anti-corrosion and anti-heat agents, which increases the service life and optimal performance of plastic products in different conditions.
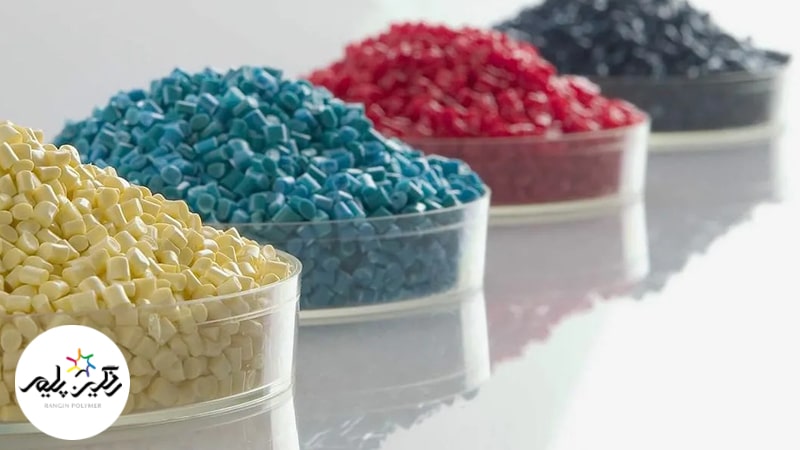
Examining the challenges and future of masterbatch
The challenges in the masterbatch industry include issues related to the supply of quality raw materials, high production costs, and the need for advanced technologies for the combination of additives and colors. In addition, maintaining the stability and compatibility of materials at different temperatures and in diverse environmental conditions is one of the major concerns of manufacturers. Also, precisely matching the masterbatch compositions to the specific needs of each industry and specific application can also be a technical challenge.
In the future, due to environmental issues and the increasing demand for the use of recycled and environmentally friendly materials, the use of green and sustainable masterbatches is expected to increase. These masterbatches not only have better performance but also reduce negative impacts on the environment. Also, with the development of new technologies, it is expected that the masterbatch production processes will be optimized and overall costs will be reduced, while the quality and variety of products will increase.
To receive additional information in this regard, please contact Rangin Polymer Company, the manufacturer of various PET masterbatches.
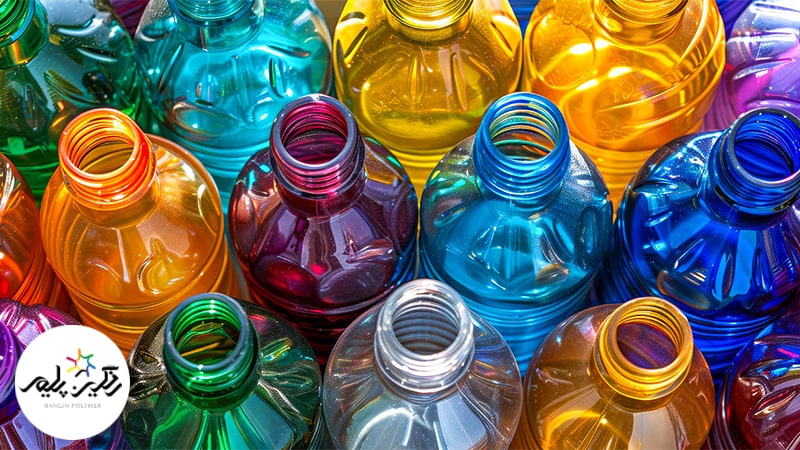
Sustainable and durable plastics
Sustainable and resistant plastics are materials that, in addition to having desirable technical and mechanical properties, are able to withstand environmental conditions and various uses. Due to the combination of special additives, these types of plastics can significantly increase the useful life of plastic products and have greater resistance to damage such as UV radiation, heat, humidity and corrosion.
Since more people’s attention has been drawn to environmental issues today, the use of sustainable plastics with properties resistant to environmental damage, including recyclable plastics or plastics made from renewable resources, has grown significantly. These types of plastics allow manufacturers to produce products with a long lifespan and minimal damage to the environment.
Conclusion
Finally, masterbatches, as efficient and effective tools in the plastics industry, play a vital role in improving the properties and quality of plastic products. From adding different colors to increasing chemical, mechanical, thermal and even anti-UV resistance, masterbatches cover a wide range of applications in various industries.
By using these materials, it is possible to simultaneously improve physical properties and reduce production costs. Companies producing various types of PET masterbatches, such as Rangin Polymer, play an important role in improving the quality and efficiency of plastic products by producing specialized masterbatches, and allow manufacturers to market products with desirable characteristics and in accordance with global standards.
Frequently Asked Questions
What is a masterbatch and what is its use?
A masterbatch is a combination of a base polymer and additives that is used to improve the characteristics of plastics such as color, strength, and physical properties.
Are masterbatches only used for coloring?
No, in addition to coloring, masterbatches can add properties such as UV resistance, heat resistance, and moisture resistance to plastics.
How do masterbatches help reduce costs?
Masterbatches reduce raw material costs and production time by reducing the need for separate additives and facilitating the production process.
Is it possible to use masterbatches to produce sustainable plastics?
Yes, masterbatches can create plastics that are more resistant and stable to environmental and chemical conditions by adding specific materials.